Optimization of delivery time and careful selection of materials
Metal Milling
Milltech has developed over the years, considerable know-how in 3- and 5-axis machining, of parts made of aluminum, titanium and in steel alloys.
Plastics Milling
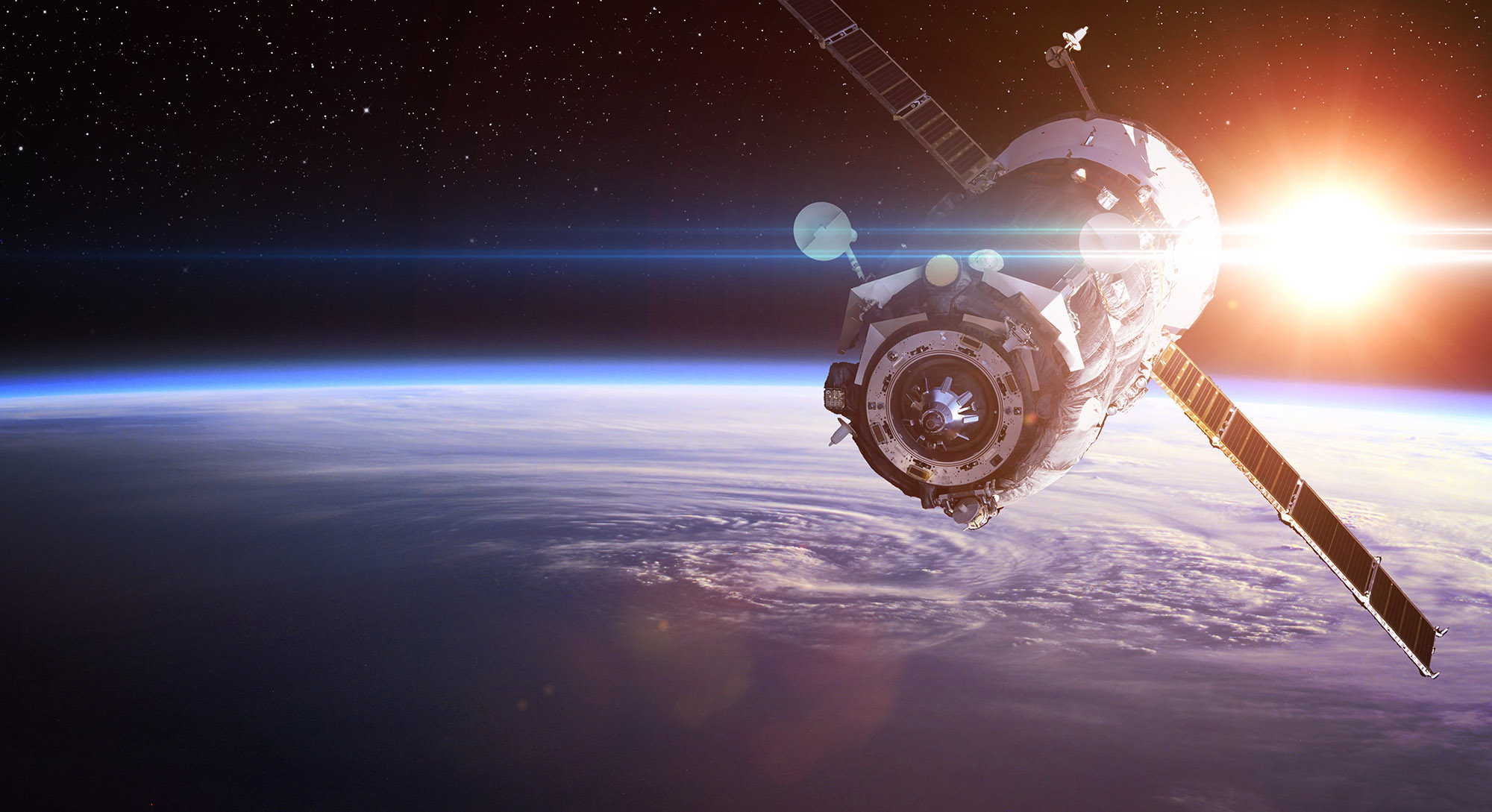
Careful operations performed by Professionals
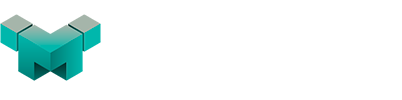
We are constantly innovating for more dynamic and attentive production
What is a milling?
In Milltech it is also possible to find the highest level of professionalism in the field of milling processing. The latter can be of two types: metal milling or plastic milling. Before analyzing in detail the difference between these two types of milling, it is essential to understand what milling is, the principle of operation and the techniques we use. Milling is a material removal machining operation that allows a wide range of surfaces to be obtained through the action of a cutting tool with a defined geometry. More precisely, mechanical milling is a machining operation by which surfaces of different kinds (such as, for example, planes, grooves, shoulders, bores, etc.) can be obtained by the rotary motion of a tool with several cutting edges. Machining is usually carried out by following several steps, starting with roughing and ending with finishing. The first part is to quickly remove a large amount of material as quickly as possible. The final part of milling, on the other hand, through the removal of a smaller volume of metal, results in a product that conforms to the design mainly in terms of size and surface roughness.Frequently asked questions
At Milltech, always attentive to the Customer’s requirements, we are able to provide good milling in really fast timeframes and with very high quality results.
For the uninitiated, milling can be used in a variety of situations and for a variety of operations including end milling, chamfer milling, surface flattening.
Milling can also be used as an alternative to drilling, reaming, countersinking, and threading to make blind holes, through holes, threads, cavities, and a wide variety of surfaces.
Usually, milling is used for creating shapes that are not symmetrical or have high complexity, such as holes, slots, pockets , grooves or three-dimensional profiles.
This is why it pays to rely on the best.
In order to achieve good milling, one must rely on a good milling machine, which is the machine tool used for mechanical milling of metals and non-metals.
In its basic form it consists of three main components: bedplate, spindle and electric motor.
The bedplate is basically the table, where the workpiece is fixed for milling, an upright, on which is placed the spindle, which comes into action thanks to the energy generated by an electric motor.
For milling, in fact, the spindle is used to impart to the milling tool, the cutter, the rotary motion that enables it to remove chips.
Milling machines can often be divided into two macro groups, established according to the orientation of the tool.
Thus we find horizontal milling machines and vertical milling machines.
The former have the spindle mounted horizontally, while the latter have the cutter oriented vertically.
The crucial node in the milling process is to establish the machining parameters.
These parameters are indispensable for obtaining a quality product.
Indeed, it is necessary to determine what the milling feed rate is, its speed and also the cutting and spindle speed.
As well as it is important to know the axial cutting depth and the radial cutting depth.
Here is a small summary useful for easy understanding of the milling parameters: Feed.
The feed distance of the cutter, during each individual rotation of the tool.
For multi-tooth milling cutters, this parameter can be obtained by multiplying the number of teeth by the stock removal of each individual tooth.
Cutting speed.
The speed of the surface to be machined relative to the tool during cutting.
It is expressed in m/min.
Spindle speed.
The rotational speed of the tool or spindle, which is expressed in revolutions per minute.
Feed speed.
The speed of the movement of the cutter relative to the workpiece.
To obtain this speed, simply multiply the cutting speed by the spindle speed.
Axial depth of cut.
The working depth of the cutter in the workpiece, again according to its axis.
This means that the greater the depth of cut, the lower the feed rate will have to be.
It is advisable to plan several passes, especially if deep cuts are to be made.
Radial depth of cut.
The depth of the tool that is measured along its radius, in the surface being cut, while the cut is being made.
As in the previous case, deep depths require low feed rates, and so multiple passes are usually made.