Metal Milling
Precision mechanical processing in 3 and 5 axes of components made from aluminum, titanium, and steel alloys.
We produce any type of component, with production batches of small, medium, and large quantities.
Metal milling for different industries
We create products for multiple sectors, foremost among themaviation, where it is common to use 7000 series aluminum or Ti6Al4V titanium to manufacture structural components of aircraft. Other important sectors include Aerospace, Motorsport, and Biomedical.
Complete project management
Raw material procurement
Carefully selecting all useful materials, with a targeted focus on the characteristics, details, and functions that each of them possesses, favoring one material over another depending on the intended purpose.
Design and manufacturing
of components, meticulous and professional, thanks to our machine body and the various machines that comprise it.
Dimensional testing
Dimensional and shape testing with a corresponding report, containing results that vary depending on the precision mechanical machining performed.
Delivery
Management of all necessary logistics processes to facilitate the Client in receiving the finished product at their facility.
Milling of various metal alloys.
At Milltech, we are capable of machining numerous metallic materials and different types of alloys through milling, ensuring maximum yield and precision on the requested products. Below are the machining processes we can perform!
When the material used for metal milling is steel, it is important to know that machinability depends on the alloying elements, heat treatment, and the chosen manufacturing process. Depending on these variables, various issues may arise that at Milltech we are expertly equipped to handle. Some problems during metal milling, particularly with steel, can include:
- If the steel is soft or low carbon: the formation of burrs and cutting edge buildup;
- If the steel is hard: chipping of the material
Regarding metal milling with stainless steel as the main material, it should be specified that we refer to two particular categories:
- Austenitic and duplex steel;
- Ferritic and martensitic steel.
The possible and main issues that may arise during metal milling with this material include surface finish, cutting edge buildup/sticking, burr formation, notch wear, and the formation of thermal micro-cracks along with the associated chipping of the cutting edges. All these problems during metal milling do not pose a real issue for us at Milltech; on the contrary, their potential presence is approached as a challenge—an additional reason to showcase our professionalism in the field and further refine our work.
In metal milling involving hardened steel, tempered to a hardness of >45 – 65 HRC, all processes related to steel inserts for molds (deep drawing), forging molds, and casting molds are included. In all these cases, the main problems that can occur during metal milling of this type are: edge breaking of the piece or abrasive wear on the side of the insert. In all these cases, the main problems that can occur during metal milling of this type are: edge breaking of the piece or abrasive wear on the side of the insert.
A separate chapter is represented by the different types of cast iron: gray, ductile, compact graphite (CGI), or austempered ductile iron (ADI). Each of these can present various issues during the metal milling process. Among the most common problems are those related to gray cast iron and compact graphite cast iron which may suffer from abrasive wear on the side and thermal micro-cracking. Additionally, the inconveniences of the machined component include chipping on the exit side of the cutter and surface finish problems. By relying on us at Milltech, you have nothing to fear. By relying on us at Milltech, you have nothing to fear.
The ISO group that includes aluminum also includes alloys based on magnesium, copper, and zinc. Therefore, when we talk about metal milling in this group, we are not referring to a single type of milling; rather, the processing will depend on various factors related to the type of material involved in metal milling in question.
The machinability of aluminum—in terms of metal milling—varies depending on the amount of silicon (Si) contained within it. In physical chemistry, a mixture of two or more substances that has a melting point lower than that of its individual components is defined as eutectic. In metallurgy, if a component’s concentration in a metallic alloy exceeds its eutectic point concentration it is referred to as hypoeutectic. In metallurgy, if a component’s concentration in a metallic alloy exceeds its eutectic point concentration it is referred to as hypoeutectic.This overview is important for correctly explaining metal milling processes for materials like aluminum that belong to the same ISO group because common aluminum is hypoeutectic when its silicon (Si) content is less than 13%. When working with this type of aluminum it is important to know that cutting edge buildup/sticking can cause burr formation and surface finish problems; additionally good chip formation and evacuation are necessary to avoid scratch marks on surfaces.Once understood what risks may arise from this kind of metal milling process for professionals like us at Milltech addressing them will not be an issue should they arise; proper study forms an excellent foundation for work which is why Milltech invests significantly in training its collaborators especially regarding processes such as metal milling and plastic milling.
The milling of titanium-based metals and heat-resistant superalloys is somewhat more complex but not impossible. Heat-resistant superalloys are referred to as HRSA and are typically classified into three groups:
- Nickel-based alloys;
- Iron-based alloys;
- Cobalt-based alloys.
Regarding titanium it can be either pure or alloyed; this variable introduces substantial differences in metal milling involving titanium depending on its type.In any case both types share a common characteristic which makes them difficult to machine especially under aging conditions.
High Precision Metal Milling
The mechanical operation of milling is a complex finishing process; for impeccable metal milling we at Milltech guarantee maximum professionalism by using modern machines particularly a technologically advanced machining center.
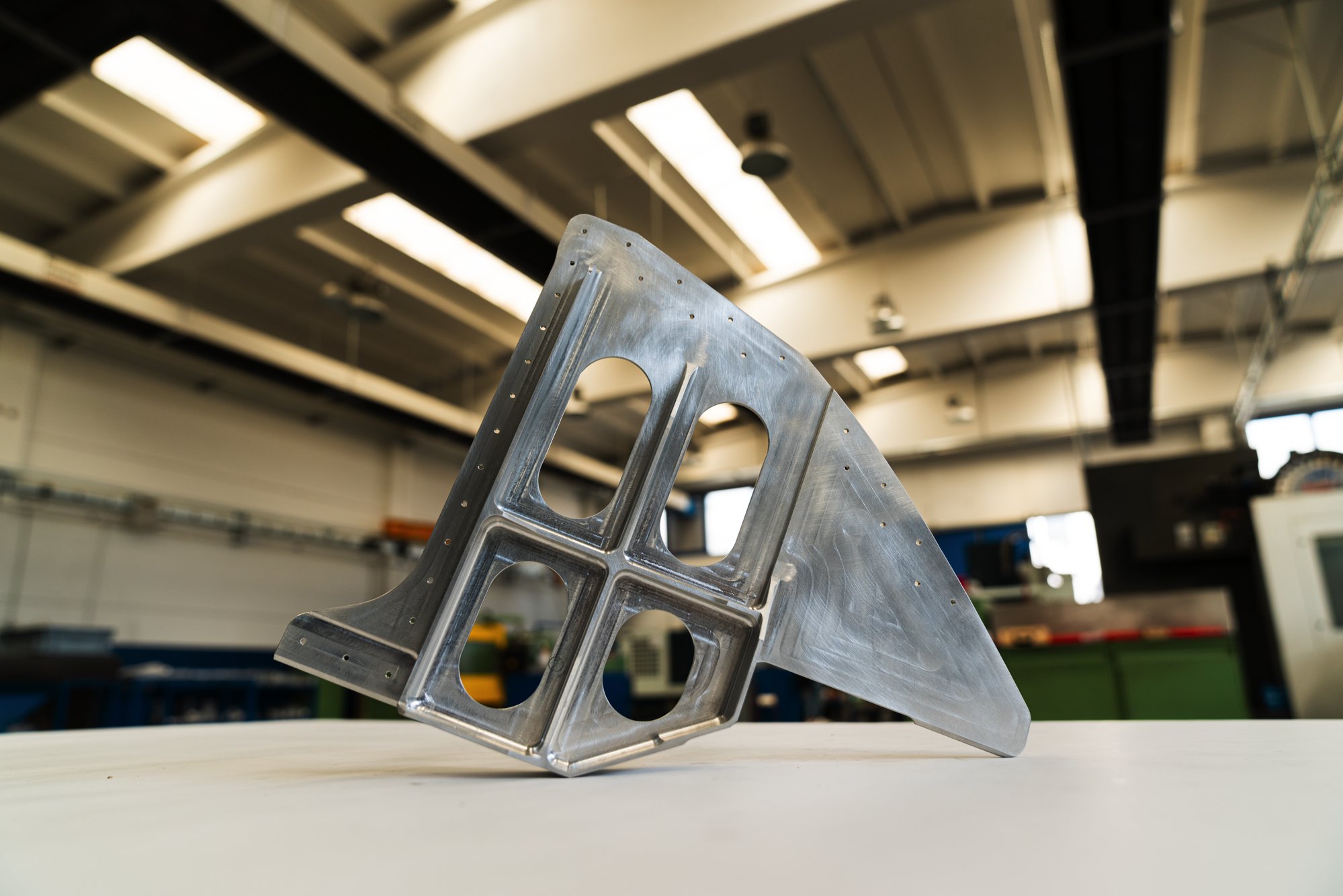
AW109
M346
Eurofighter
Absolute Precision Mechanical Machining
The mechanical processing method that allows for shaping different pieces of metallic materials into flat or complex forms is known as metal milling; work is performed using a specialized machine called a milling machine.
The metal milling process requires rotation from a defined geometry cutting tool mounted onto a spindle along with simultaneous movement from motorized axes but understanding characteristics within materials being machined helps select suitable cutters/inserts accordingly.The metal milling process requires rotation from a defined geometry cutting tool mounted onto a spindle along with simultaneous movement from motorized axes but understanding characteristics within materials being machined helps select suitable cutters/inserts accordingly.
Thus processes begin selecting inserts since their specific qualities optimize tool life & quality surfaces produced when choosing one must keep three fundamental parameters in mind:
- Material component: different ISO groups including materials like steel stainless-steel cast iron;
- Type working method: finishing medium machining roughing
- Working conditions: good average difficult.
Specific qualities within inserts combined right parameters allow optimizing tool life and quality surfaces produced based upon what’s being processed different reactions/issues may arise.
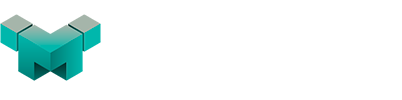
Advanced Metal Milling Processing
At Milltech it is easy to grasp most important characteristics regarding processing metals due high precision from our collaborators & machines therefore we rely best professionals industry who possess extensive experience alongside innate passion for their work.